Customized Product Tour Exhibition · High-Precision Machining of New Energy Vehicle Motor Casing
May 16,2024
Customized Product Tour Exhibition
Focus on developing applicable solutions
High-Precision Machining of New energy Vehicle Motor Casings
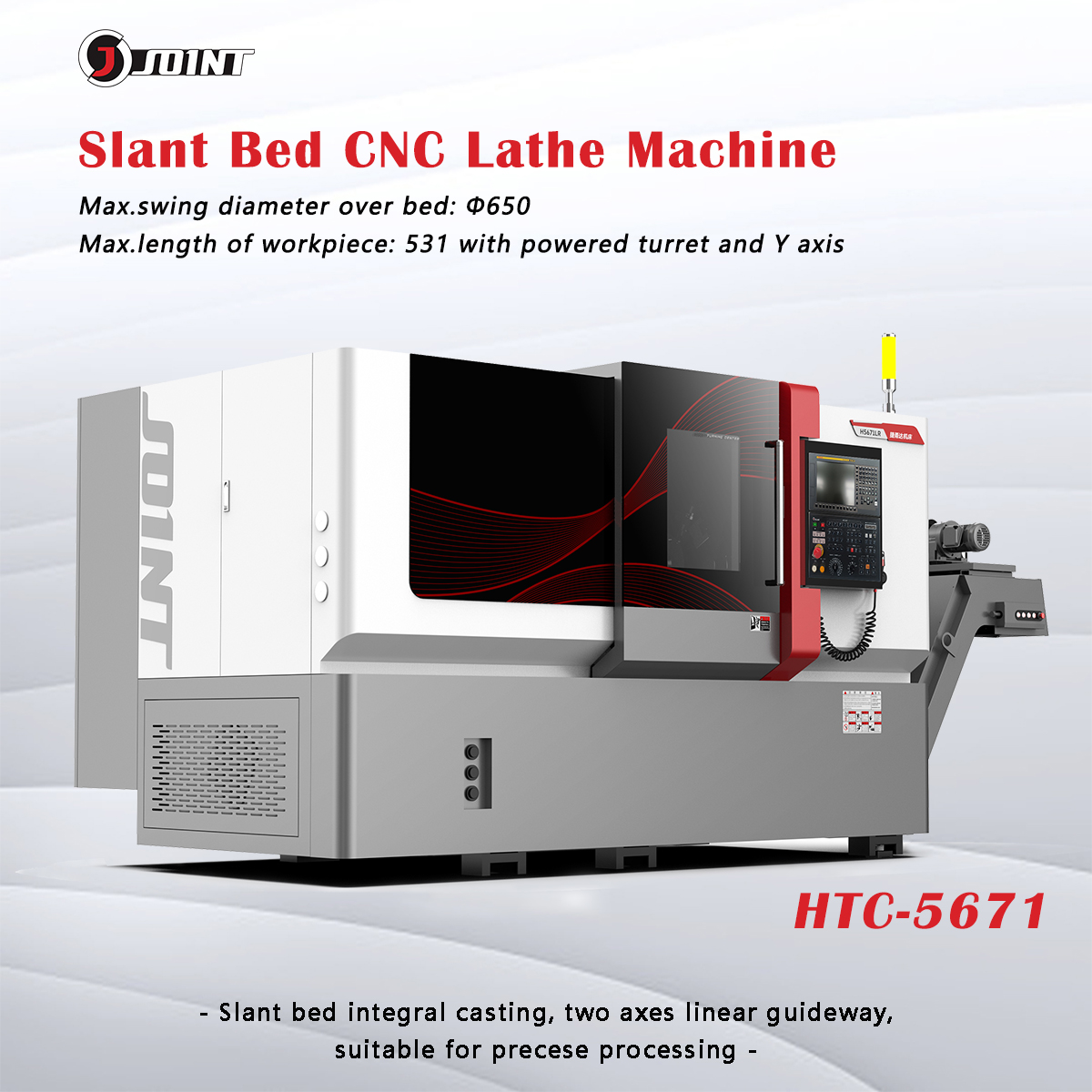
The turning and milling compound machine is used to optimize the cutting tools and processes, merge multiple processes, and complete the turning and milling processing in one clamping, nearly doubling the processing efficiency.
2.Precision control of eccentric workpiece processing
The eccentric structure of the workpiece: it will lead to greater inertia, resulting in a large roundness deviation of the processing inner cavity (generally 0.03-0.05mm).
The material is soft and prone to tool vibration: The workpiece material is soft and the tool vibration is prone to occur during processing, which affects the surface roughness and processing accuracy.
In response to the above problems, the main spindle box, spindle, and body structure of the CNC lathe were designed and modified, which greatly improved the cutting rigidity and the stability of the entire machine during large inertia rotation.
3. Thin-wall variant and eccentric inertia fixture design
Through point clamping, eccentric balancing and other methods, the fixture design problems of thin-wall clamping and eccentric clamping are solved. The accuracy of deep cavity processing is stable within 0.02mm, and the end hole is within 0.009).
4. Better finish for deep cavity processing
Thin-walled deep cavity machining: During deep cavity machining, the tool is easily affected by cutting forces, which affects the machining accuracy and poor finish.
Select tools suitable for deep cavity machining, and determine the optimal cutting parameters through multiple experiments to reduce the stress on the tools and improve the stability and smoothness of the machining.
This solution has also been applied to other processing areas such as valve body parts.

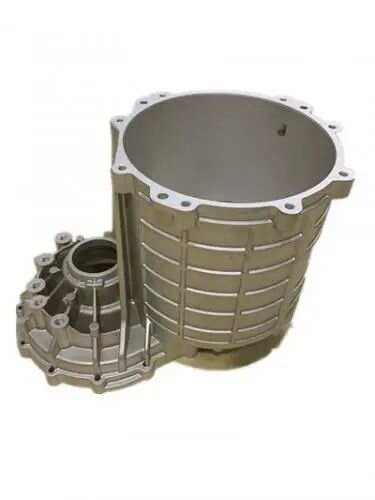

Focus on developing applicable solutions
High-Precision Machining of New energy Vehicle Motor Casings
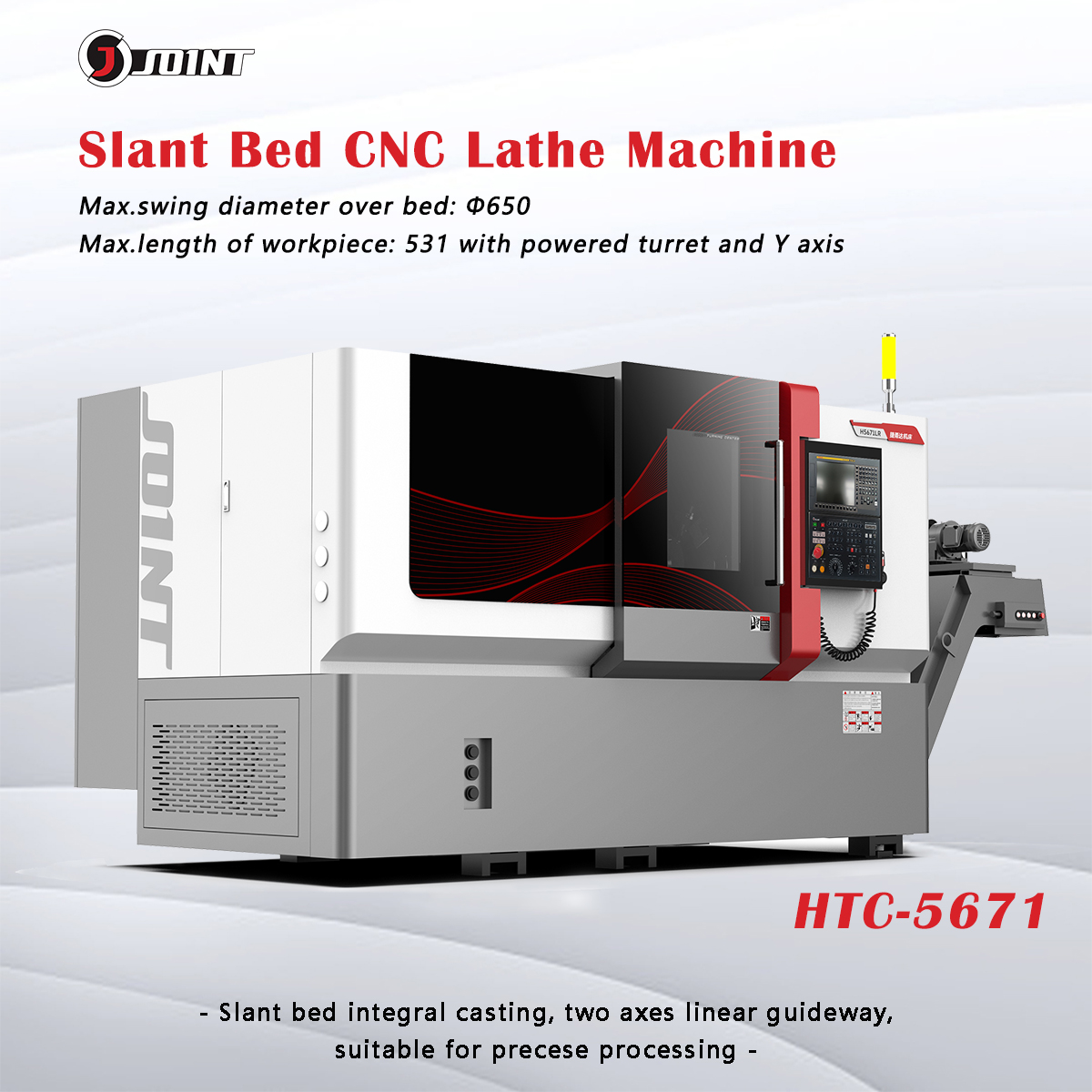
- Customer background and needs
- Technical difficulties and challenges
The turning and milling compound machine is used to optimize the cutting tools and processes, merge multiple processes, and complete the turning and milling processing in one clamping, nearly doubling the processing efficiency.
2.Precision control of eccentric workpiece processing
The eccentric structure of the workpiece: it will lead to greater inertia, resulting in a large roundness deviation of the processing inner cavity (generally 0.03-0.05mm).
The material is soft and prone to tool vibration: The workpiece material is soft and the tool vibration is prone to occur during processing, which affects the surface roughness and processing accuracy.
In response to the above problems, the main spindle box, spindle, and body structure of the CNC lathe were designed and modified, which greatly improved the cutting rigidity and the stability of the entire machine during large inertia rotation.
3. Thin-wall variant and eccentric inertia fixture design
Through point clamping, eccentric balancing and other methods, the fixture design problems of thin-wall clamping and eccentric clamping are solved. The accuracy of deep cavity processing is stable within 0.02mm, and the end hole is within 0.009).
4. Better finish for deep cavity processing
Thin-walled deep cavity machining: During deep cavity machining, the tool is easily affected by cutting forces, which affects the machining accuracy and poor finish.
Select tools suitable for deep cavity machining, and determine the optimal cutting parameters through multiple experiments to reduce the stress on the tools and improve the stability and smoothness of the machining.
- User effectiveness and social benefits
This solution has also been applied to other processing areas such as valve body parts.

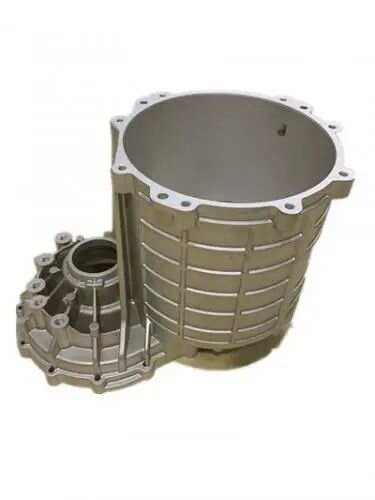
